Production process
We carefully follow
every single step
The technical department realizes new projects studied and developed with the use of 3D parametric programs, then sampling is carried out in order to test and certify the product. Following the positive outcome of the tests we move to series production composed of: mechanical turning operations by means of numerical control lathes and milling with multi-axis machining centers; tig and mig welding by robot; mechanical finishing and polishing. Once the necessary processing have been completed, all the components, stored in automatic vertical warehouses, are picked up and assembled according to each order specifications. Valves, once assembled, are 100% tested and then registered.
The entire production process is constantly monitored by quality control.
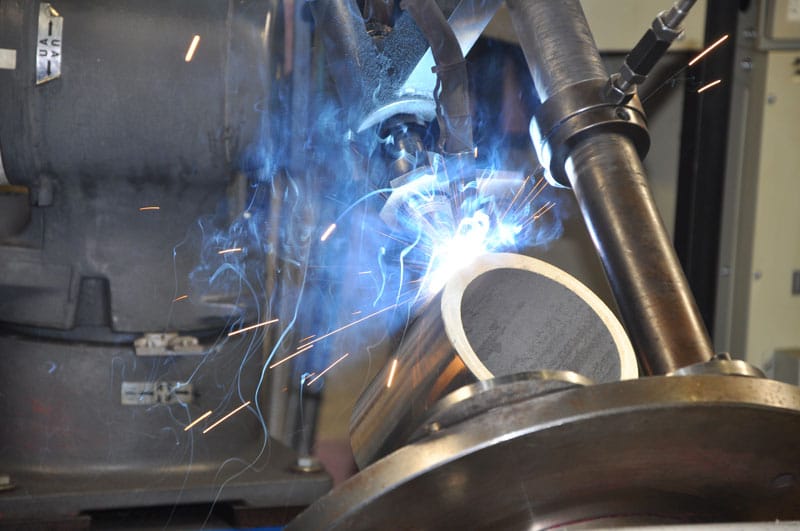
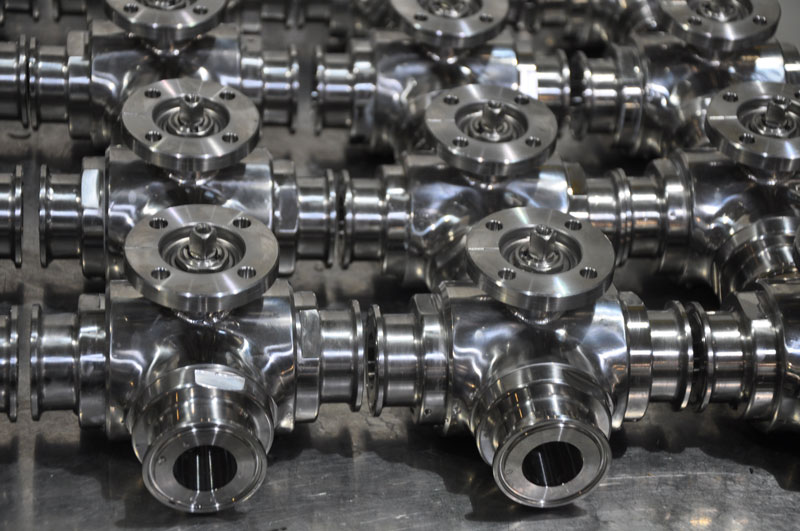
A process with attention to detail
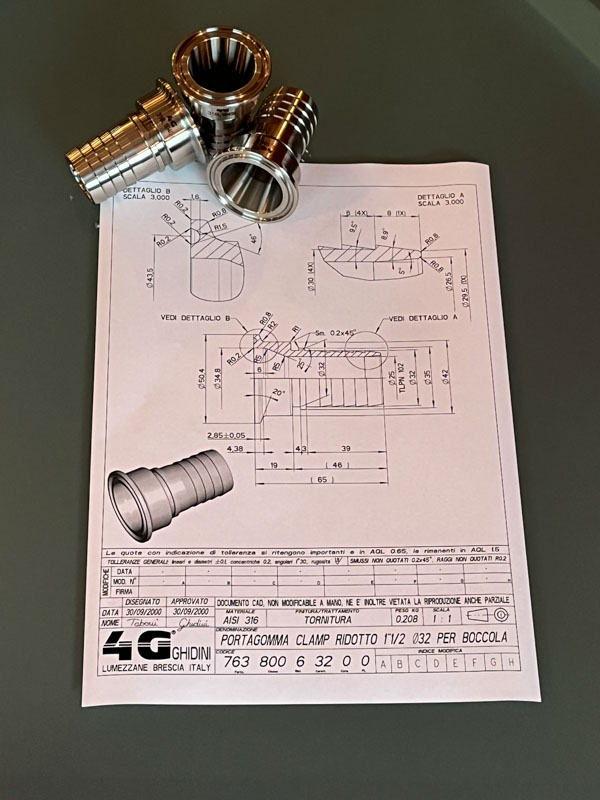
Design
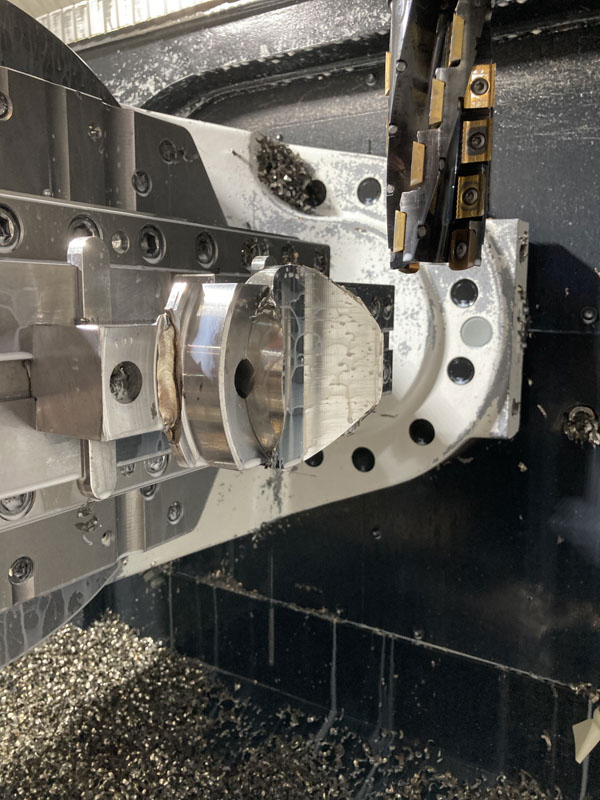
turning and milling
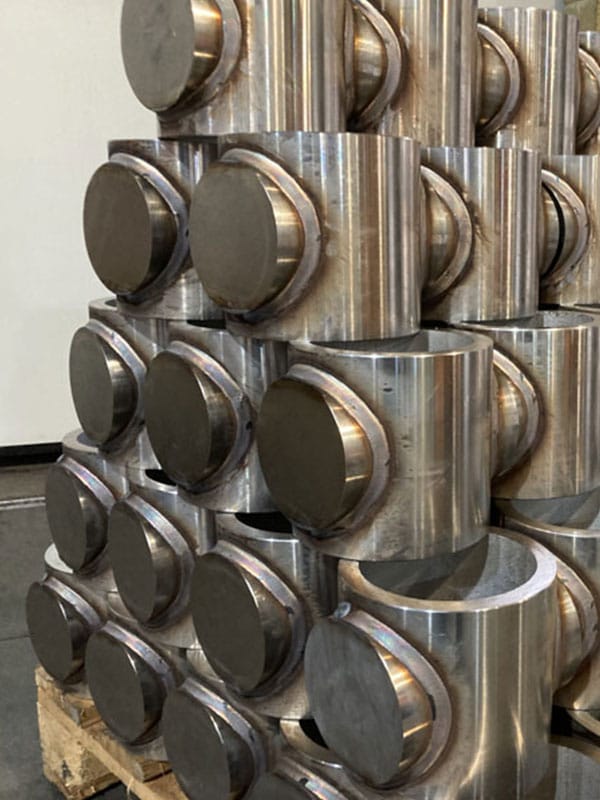
welding
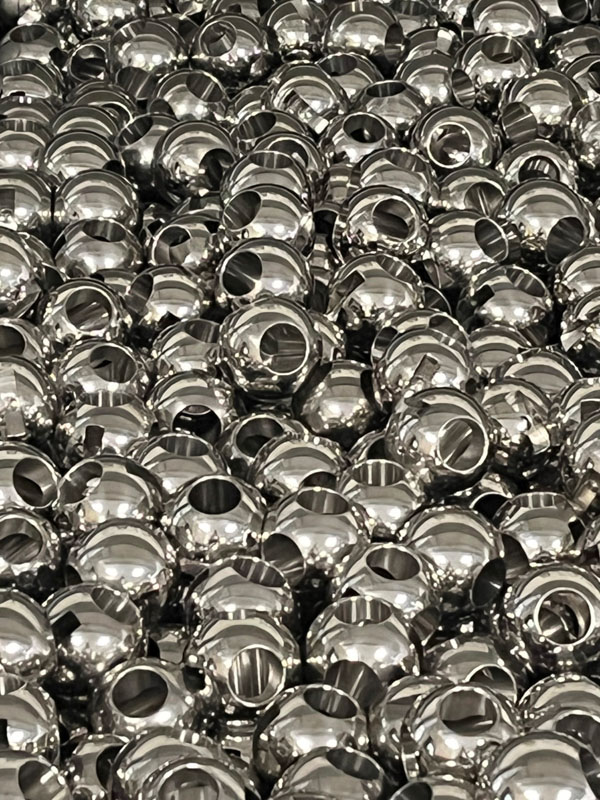
finishing
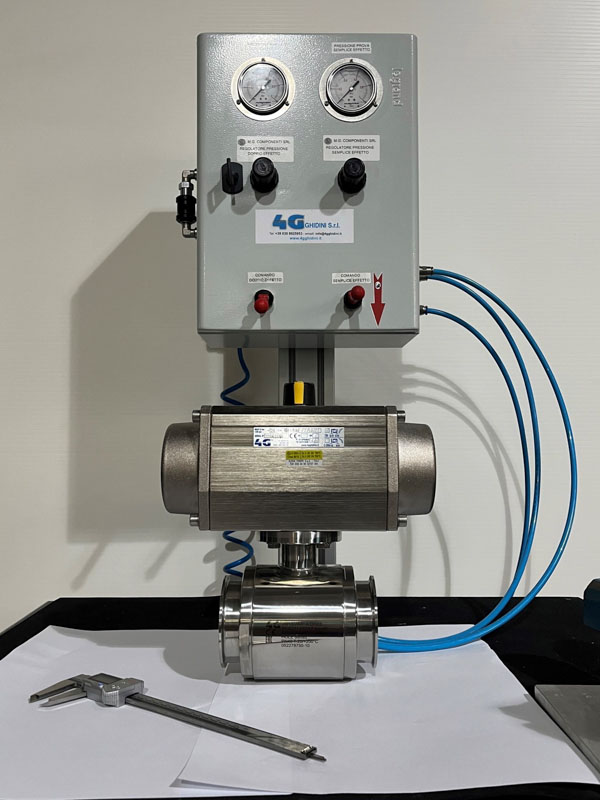
assembling and testing
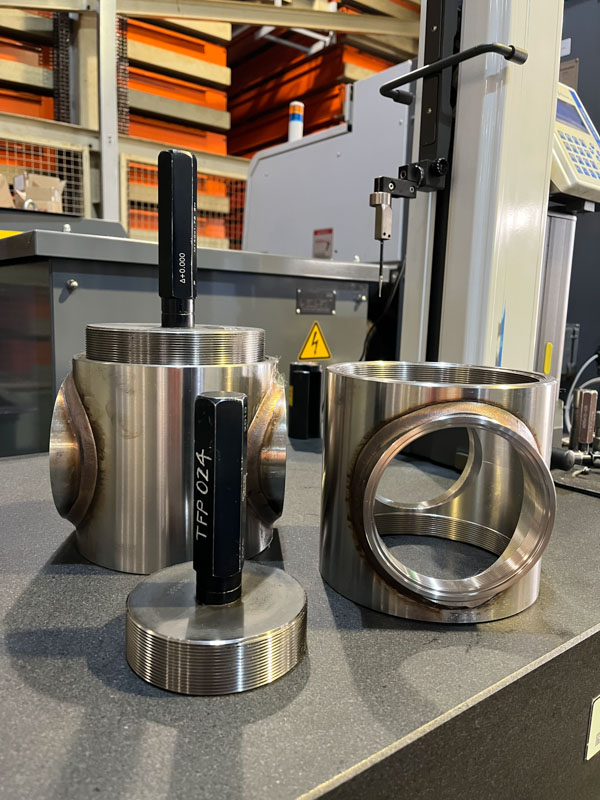
Quality control
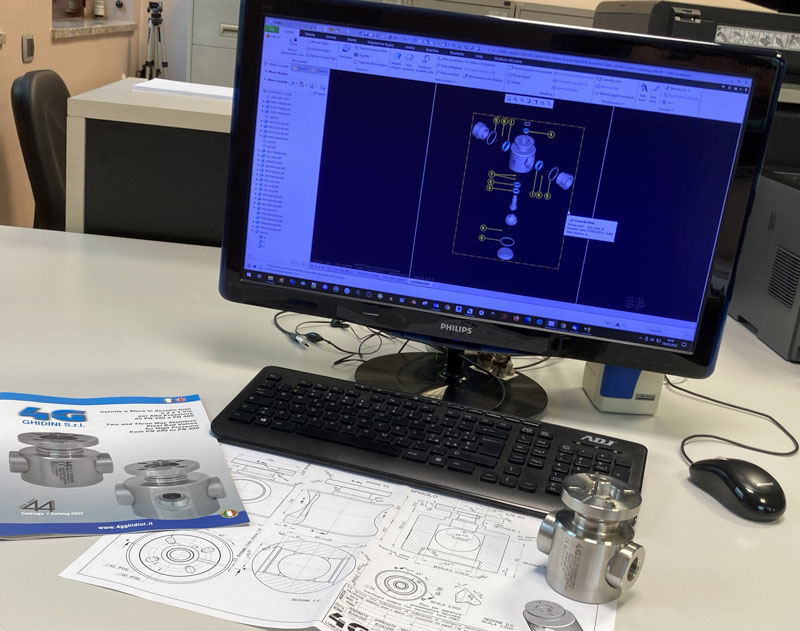
Design
The creation of 4G® GHIDINI stainless steel ball valves and fittings begins with design and development of the new item by our technical department by means of 3D parametric programs.
Subsequently, the production of a pre-series necessary to define and optimize the production cycle and carry out the related tests aimed at obtaining product certification takes place.
Turning and milling
All our products are made from bar by means of mechanical operations for chip removal with the aid of latest generation machinery such as numerical control lathes and multi-axis milling centers.
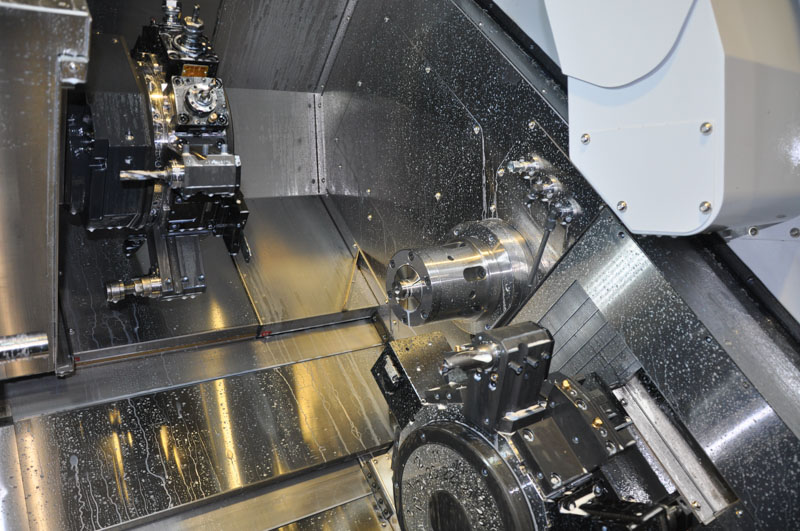
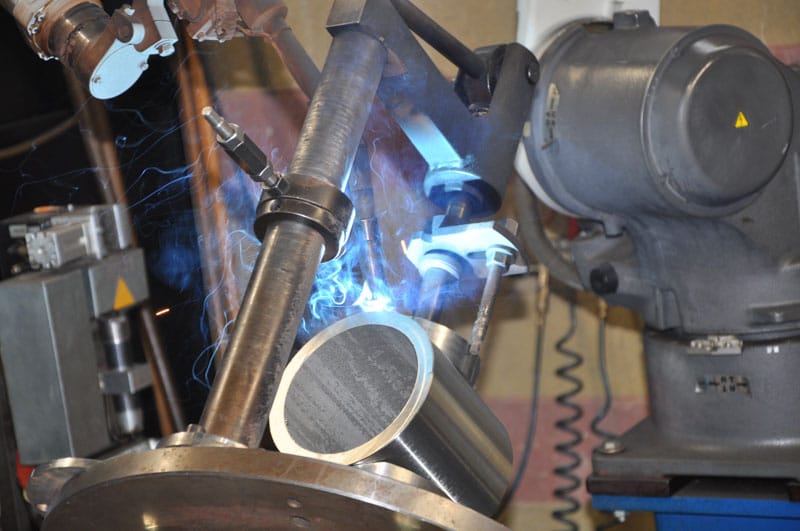
Welding
Tig and mig welding of semi-finished products takes place by robots that allow the union of several components of different sizes and geometries in order to obtain a complex valve body.
Finishing
The various components then pass to the finishing department where through mechanical polishing they acquire the peculiar brilliance that distinguishes our ball valves. The obtained pieces, before being stored in the warehouse, are subjected to a washing and degreasing treatmen.
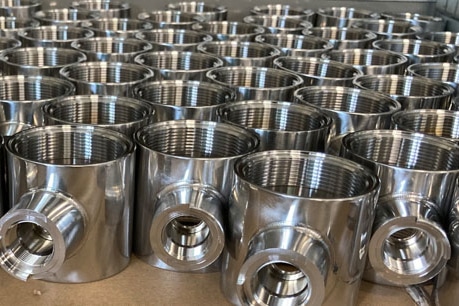
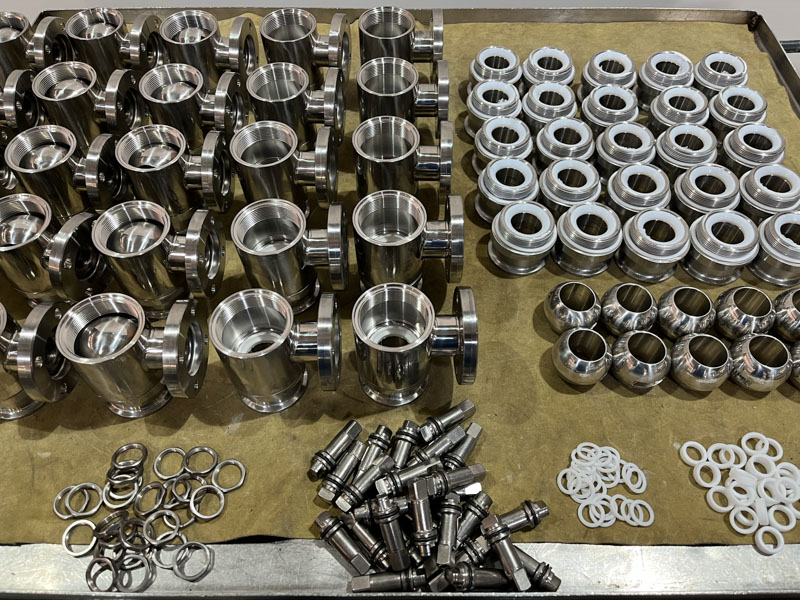
Assembling and testing
The components, stored in automatic vertical warehouses, are picked up and assembled according to each order specifications; subsequently, our ball valves are 100% tested and, following a positive result, laser marked with descriptive and use information and serial number in order to ensure traceability.
Quality control
The entrire production process is monitored by quality control, from the entry of raw materials to the subsequent processing, up to the finished product.
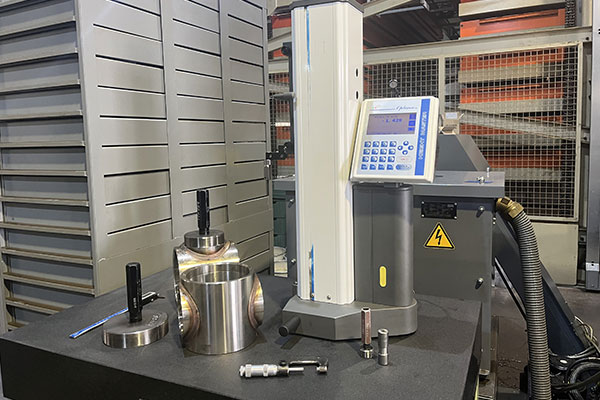
A complete range of valves
Our products catalogue consists of 2 and 3 way with “T” o “L” bore hand operated or ISO 5211 for actuator ball valves in aisi 304L and 316L stainless steel from bar, pin valves, rate valves and gauge cocks, fittings in aisi 304L and 316L stainless steel from bar, single or double acting pneumatic actuators in aluminium and stainless steel, limit switch boxes and solenoid valves.
All the available connections comply with international regulations.
Standard or integral seals in modified virgin PTFE, PTFE with glass, PTFE with carbographite, PTFE with inox, UHMW and Devlon.
Temperature range -45+200°C and pressures from PN10 to PN400.
ATEX II 2 G-D T4 zone 1-21.